LGS Removal on Active Drill Site by ESC
Ground Effects successfully deployed the Electro Separation Cell Technology to treat spent fluid at an active drill site in Northern British Columbia, Canada. Low gravity solids in the feed mud, totaling 21%v/v, were reduced to 2%v/v. The recovery rate of the base oil was 65% of the available oil from the original fluid.
The Situation
The isolated areas within the Montney unconventional reservoir make drilling operations time consuming and expensive. These areas often have limited infrastructure and operating capabilities. Disposal of waste often involves transporting material large distances, to expensive disposal facilities. This in turn drives up the overall cost of drilling.
Extended reuse of drilling fluid systems results in extensive accumulation of low gravity solids (LGS) to the point where they cannot be removed by conventional solids control equipment. Buildup of ultra fine LGS can create serious issues. Failure to adequately address these can results in excessive cost overrun or even loss of the well.
Typical options to reduce this risk are to dilute the fluid system, creating three or four times the original volume, or disposing of the fluid system and building a new system from scratch. Both options are extremely expensive. In Northern BC, major issues arise that affect the drilling operations such as reducing the rate of penetration, differential stick of the drill pipe and loss circulation can cause substantial time lost, further increasing the cost of drilling.
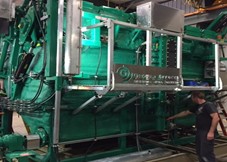
The Solution
The Electro Separation Cell (ESC) technology, recovers valuable base oil for reuse and/or resale. The ESC uses electrokinetics to destabilize the bonds within the OBM emulsion and separates out the base oil from the native clays and drilling solids. The ESC focuses on colloidal and ultra fine LGS of less than 6 microns. The result is clean base oil.
The reduction in costs and improvement of operational efficiencies is substantial. There is a 60-70% reduction of waste produced, reducing storage, disposal and transportation costs.
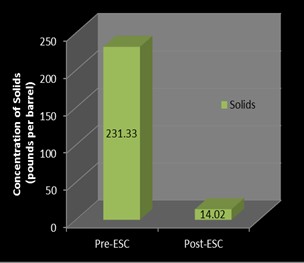
The 10M Results
Other key performance indicators achieved by the ESC Technology during this treatment process were:
- Recovered oil quality unchanged from original
- OBM properties
- before ESC: 73/6/21 %oil/%water/%solids
- after ESC: 98/0/2 %oil/%water/%solids
- Approximately 48,717kg of solids removed per day, 10M system
- Density of recovered base oil 7.16ppg
- Processing Rate between 11-22GPM (377 and 754 bbl per day), equivalent 42-83LPM (60-120m3 per day), equivalent
- Recovered base oil now available for dilution of other drill fluids
- Disposal volumes reduced by 60- 70%
- Reduced the costs and liability associated with storage, transportation and disposal of full fluid volume
- Proven, viable solution for dealing with high LGS content fluid systems
The ESC technology treated spent OBM on an active drill site in Northern BC, Canada.
- LGS in feed mud reduced from 21% to 2%v/v
- 48,717kg of solids removed per day, 10M
- Final density 7.16ppg
- Process rate 60 to 120 meters3 per day equivalent
- Disposal volumes reduces by 60 to 70%
ESC Run Capacity per Unit | 1M | 3M | 5M | 10M |
---|---|---|---|---|
Gallons per minute (GPM) | 1.1 to 2.2 | 3.3 to 6.6 | 6 to 11 | 11 to 22 |
Barrels per day (BPD) | 38 to 76 | 113 to 226 | 189 to 377 | 377 to 755 |
Liters per minute (LPM) | 4 to 8 | 12.5 to 25 | 21 to 42 | 42 to 83 |
Cubic meters per day (m3/day) | 6 to 12 | 18 to 36 | 30 to 60 | 60 to 120 |